螺釘預緊力是超精密加工與裝配中不可忽視的重要因素,基于 ANSYS接觸分析模塊,采用具有回轉(zhuǎn)對稱結(jié)構(gòu)的多個平行環(huán)形圓臺結(jié)構(gòu)代替螺紋的螺旋升角結(jié)構(gòu),建立了具有工程實際參考意義的螺紋計算分析模型,通過有限元分析,計算得到了螺釘預緊力作用下連接件及螺紋牙型的變形特征。
螺紋的預緊有利于增強聯(lián)接的剛性、緊密性、防松及防滑[1],以防止受載后被聯(lián)接件間出現(xiàn)縫隙或相對滑移。預緊力的適當控制是確保螺紋聯(lián)接質(zhì)量的關(guān)鍵,預緊力過小將導致聯(lián)接松動而失效,過大的預緊力又會使聯(lián)接件在裝配變形或偶然過載時被拉斷[2]。
研究人員對螺釘預緊力的關(guān)注重點主要集中于螺釘?shù)氖?、預緊力模型及工程控制方法等,對螺釘?shù)哪P吞幚磉M行了較大簡化[5],對螺釘預緊力造成螺紋牙型變形等裝配過程零件內(nèi)部變形缺乏有效的關(guān)注。
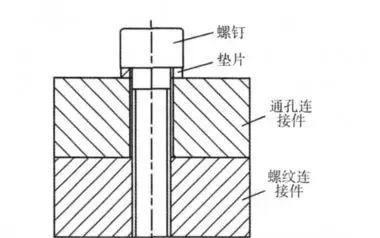
圖1 計算模型
為了簡化所分析問題的復雜程度,便于探索其中蘊含的科學規(guī)律,同時又不失一般性,計算所用幾何模型采用具有回轉(zhuǎn)對稱的結(jié)構(gòu),如圖1所示。模型由兩個被連接件:通孔連接件、螺紋連接件和螺釘、墊片組成,螺釘公稱直徑M8,通孔連接件尺寸為準50×20,中心通孔直徑為準9,螺紋連接件尺寸為準50×20,中心有一M8 螺紋通孔,墊片的外徑為準16,內(nèi)徑準9,厚度1.6。由于螺釘預緊力與擰緊力矩之間的關(guān)系已經(jīng)較為成熟[6],直接給定螺釘?shù)念A緊力5kN,對各聯(lián)接件的變形進行分析。
研究的重點是分析在螺釘自身的拉緊力作用下,被連接件的整體變形,及較為薄弱的螺紋部分的應力及變形問題。由于螺紋部分的應力與變形相對較大,因此如需對物理問題的深入分析,必須以能充分反映實際結(jié)構(gòu)的模型進行計算,最理想的模型即是建立符合國標要求的實際螺紋幾何模型,然后再進行相應的應力應變分析,計算結(jié)果才具有說服力。
不過,由于實際螺紋的幾何模型較為復雜,幾何實體建模存在較大難度,由于螺旋升角的存在,螺紋接觸牙型表面的法向矢量隨著位置的不同各不相同,即便在三維建模軟件UG中也難以構(gòu)建出正確的模型。即便在三維建模軟件中能構(gòu)建出正確的實體模型,由于螺紋之間的相互作用屬于接觸分析范疇,在ANSYS接觸分析中,如果接觸面或目標面整個螺紋均為螺旋表面,則接觸面的法向矢量會出現(xiàn)一會兒指向外部,一會兒指向內(nèi)部的矛盾之處,使ANSYS難以實現(xiàn)正確、有效的問題求解。為了突出分析問題的特征,又不失問題分析的可行性,需對螺紋結(jié)構(gòu)進行簡化。簡化方法如下:保留螺紋的牙型角等結(jié)構(gòu)尺寸不變,用多個平行的環(huán)形圓臺結(jié)構(gòu)代替螺旋升角結(jié)構(gòu),如圖2所示。螺紋螺距、牙型等結(jié)構(gòu)參數(shù)均保持不變,并按國標進行建模。這種簡化方法一方面簡化了螺紋模型,另一方面又充分的體現(xiàn)了內(nèi)、外螺紋之間接觸應力及實際變形情況,計算結(jié)果具有一定實際意義和指導作用。

由于被連接件及螺釘均為軸對稱結(jié)構(gòu),因此在ANSYS 中可用平面單元PLANE42代替實體單元進行建模與分析,從而可以簡化建模過程,而且便于利用APDL 語言對建模與計算過程進行控制。據(jù)此在ANSYS中建立的計算模型,如圖3所示。由于螺紋牙型部分的尺寸尺度與其它尺寸相比小得多,而螺紋牙型的變形又是關(guān)注的重點,須將螺紋部分的網(wǎng)格細化,得到劃分網(wǎng)格后的有限元模型,如圖4 所示。設置螺釘軸線為軸對稱邊界條件并限制水平方向位移,墊片的上平面各項位移為0,螺釘軸線豎直向上受集中載荷5kN。
各相互配合的內(nèi)外螺紋牙型面及通孔連接件與螺紋連接件之間創(chuàng)建接觸對進行約束。

所有零件材料均為鋼,計算參數(shù)為:彈性模量E=150GPa,泊松比P=0.3,密度Den=7830kg/m3。
位移
由螺釘拉緊造成的各連接件的變形位移,如圖5 所示。從圖5 中可以看出,在螺釘拉力的作用下,被連接件中心受壓產(chǎn)生變形和位移,而被連接件的外圓柱面邊緣則因受到擠壓產(chǎn)生翹曲,造成外緣彼此脫離的現(xiàn)象。
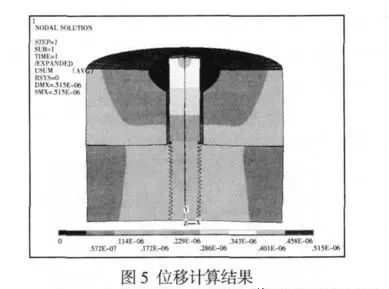
重點關(guān)注被連接零件的變形,尤其是內(nèi)螺紋零件的變形。從圖5中可以看出,螺紋連接件中心近螺紋處的位移最大,從計算結(jié)果中提取螺紋連接件的最大位移,為0.16μm。由于被連接件外緣彼此產(chǎn)生脫離,分別提取兩個被連接件外緣接觸點的位移,進行相減可得對應的脫離距離。從提取結(jié)果可以看出,被連接件在X和Y方向均發(fā)生錯位與脫離現(xiàn)象,其中,X方向最大脫離0.014μm,Y方向最大脫離0.033μm。
應力與應變
由螺釘拉緊造成的各連接件的應力云圖,如圖6所示。應變云圖,如圖7所示。
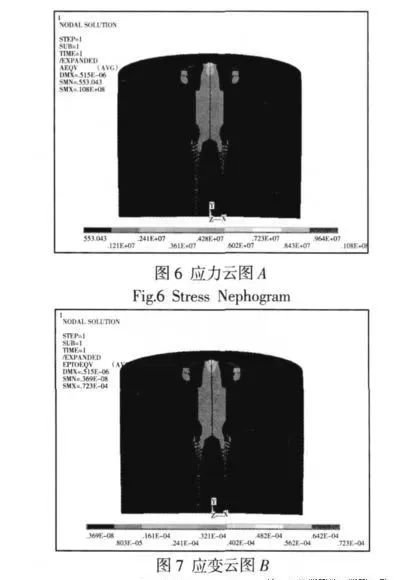
由于給螺釘施加的是集中載荷,因此計算顯示螺釘?shù)闹行奶幍膽εc應變均最大,由于這點不作為分析重點,因此暫不作細致分析。而對螺紋接觸部分而言,螺紋擰入的前幾個牙型彼此產(chǎn)生比較大的應力和應變,有比較大的應力集中。對于被連接件而言,由于作用面積較大,應力和應變相對而言顯得比較小。
螺紋的變形
將螺紋連接接觸配合部分的應力計算結(jié)果放大顯示,如圖8所示。從圖8中可以看出,螺紋的擰入的前幾個牙型彼此之間產(chǎn)生比較大的應力和變形,有比較大的應力集中,而其余的螺紋牙型則對螺紋拉力的貢獻較小。
而螺紋口處的應力集中與變形最大,螺紋越深,螺紋牙型的應力與變形逐漸減小,本例的計算結(jié)果顯示,主要有前六圈牙型對螺釘預緊力做出貢獻。從這點可以看出,從結(jié)構(gòu)設計角度考慮,可對螺紋的擰入深度進行適當優(yōu)化。

從螺紋牙型的接觸變形可以看出,被連接件內(nèi)螺紋受螺釘外螺紋的壓力作用產(chǎn)生Y方向的變形,螺釘則產(chǎn)生Y方向的位移,因此螺紋主受力面產(chǎn)生接觸與摩擦,而副受力配合面則發(fā)生脫離。這種現(xiàn)象與定性分析及理論結(jié)果一致,表明分析結(jié)果具有一定的可信度。螺釘預緊力的影響與控制在超精密加工與裝配中是不可忽視的重要因素,基于ANSYS接觸分析模塊,通過對螺釘進行適當簡化,建立了具有實際參考意義的工程化螺釘預緊力及連接件變形的分析模型,通過有限元分析與計算,得到了連接件及螺紋牙型的變形特征:
(1)在螺釘預緊力的作用下,被連接件螺紋孔中心部分受壓產(chǎn)生變形,而被連接件的外圓柱面邊緣則因受到擠壓產(chǎn)生翹曲和彼此脫離的現(xiàn)象;
(2)螺釘預緊力主要由螺紋擰入深度較淺的前幾個牙型貢獻反作用力,其彼此之間產(chǎn)生比較大的應力和變形,有比較大的應力集中,而其余的螺紋牙型則對螺紋預緊拉力的貢獻較小。螺紋口處的應力集中與變形最大,螺紋越深,螺紋牙型的應力與變形逐漸減小。
計算分析結(jié)果既考慮了裝配零件的宏觀變形,又展現(xiàn)了螺紋牙型細微結(jié)構(gòu)的應力與變形情況,具有很強的工程應用價值,可為精密零件的結(jié)構(gòu)設計和螺釘預緊力控制等裝配工藝提供指導。